Education

MS in Mechanical Engineering
The University of Maine
2018 - 2020
Thesis: Design and fabrication of a 3-dimensional capacitive-based force sensor
Relevant Coursework: Robot Dynamics and Control, Advanced Robotics, Embedded Systems, Industrial Computer Control, Engineering Optimization, Aircraft and Auto Structures

BSc in Mechanical Engineering
Khulna University of Engineering & Technology
2010 - 2014
Project: Design and construction of a model of a magnetic train
Relevant Coursework: Servo Mechanism & Control Engineering, Aircraft Flight Dynamics, Automobile Engineering, Aerodynamics, Machine Design, Electrical Engineering & Electrical Machines, Electronics, Computer Languages
Research Experience
Graduate Research Assistant
Biorobotics and Biomechanics Lab, UMaine
2018 - 2020
- Developed a 3-dimensional capacitive-based force sensor for gait analysis
- Developed an FEA-based framework for customization of capacitive-based force sensors
- Supervised a team of 5 undergrad students to develop a robotic manipulator for calibration of force sensors
- Collaborated with a lab member to develop a digital capacitance measurement system
Teaching Experience
Graduate Teaching Assistant
The University of Maine
2018 - 2020
Courses: Model, Analysis, and Control of Mechanical Systems, Modern Control Sytem Theory & Application, Mech Lab I, & II
Instructor
Brahmaputra Polytechnic Institute
2014 - 2018
Courses: Applied Mechanics, Applied Mathematics
Publication
Rahman, M. S., and Hejrati, B. (March 2, 2022). “A Low-Cost Three-Axis Force Sensor for Wearable Gait Analysis Systems.” ASME. J. Med. Devices. June 2022; 16(2): 021012. https://doi.org/10.1115/1.4053725
Presentation
Biomimetics, Artificial Muscles & Nano-Bio (BAMN 2019) “A Wearable 3-Dimensional force
measuring sensor for gait analysis applications.”
International Conference on Mechanical, Industrial & Energy Engineering (ICMIEE 2014) “Design
and Construction of a Model of a Magnetic Train.”
Project
Design and fabrication of a 3-dimensional capacitive-based force sensor
- Performed structural and electro-mechanical analyses in COMSOL to design the sensor
- Designed the parts using SolidWorks and built test prototypes using a 3D printer
- Generated G-codes using Fusion 360 and fabricated the final parts using a CNC machine and machine shop tools
- Designed the printed circuit board (PCB) using EasyEDA and soldered the components on the PCB board
- Programmed the microcontroller to collect and transmit capacitance data using I2C and UART communication
- Calibrated the sensor and performed evaluation tests to assess the performance of the developed sensor
A robotic manipulator for applying 3-directional force
- Modified the design of the end-effector and built it using a 3D printer
- Used Arduino to control the motion of the manipulator and collect data from force sensors to measure the applied force
Temperature Logger
- Used a temperature sensor to measure temperature and a 4 digit 7 segment display to show the current temperature
- Used a Raspberry Pi as a web server and published temperature readings on a web page
Automation of a water treatment system
- Used Autocad Plant 3d to model the water treatment plant and RSLogix Micro for PLC programming
- Used Wonderware to design the human machine interface (HMI) and Microsoft SQL Server for data extraction
Volunteer
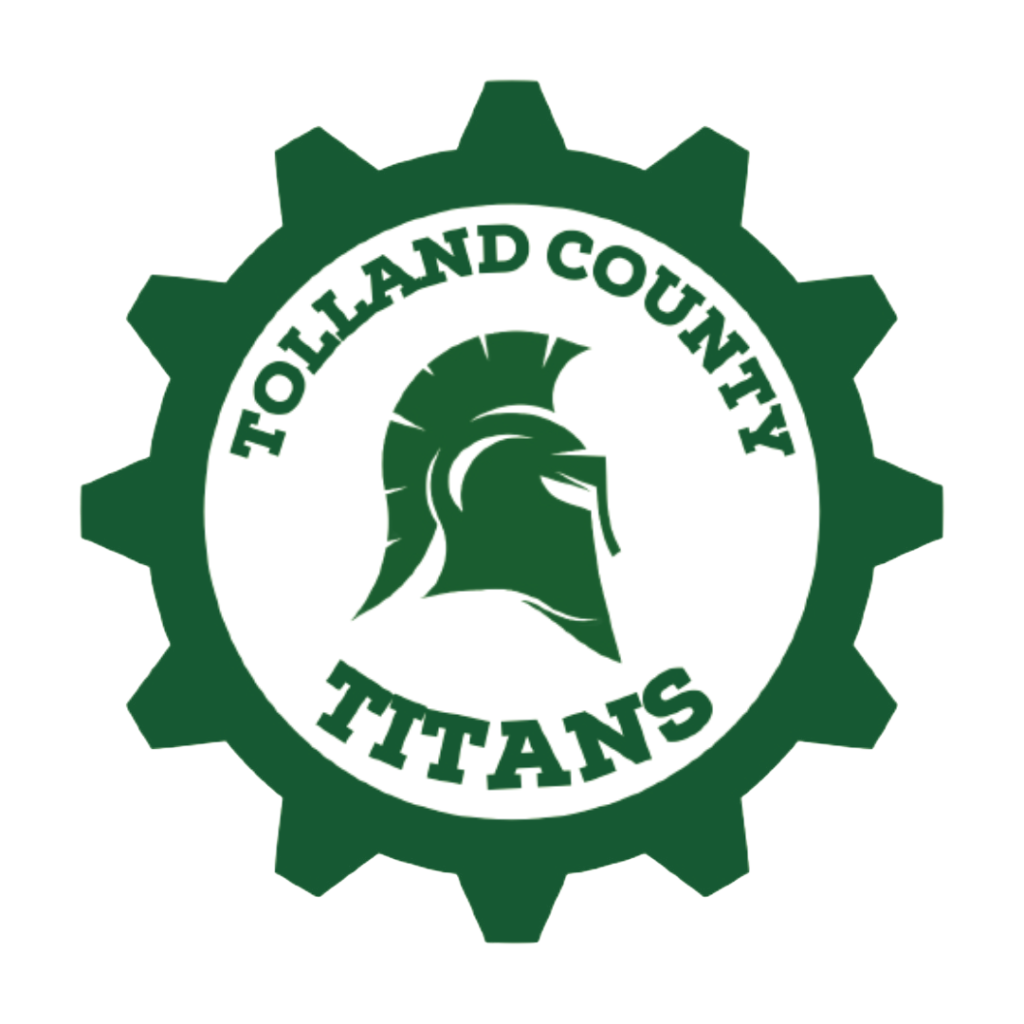
Mentor, FIRST Tech Challenge
Tolland County Robotics Foundation
- Prepare lesson plans to teach programming language and guide to write codes for robots
- Collaborate with other mentors to integrate software and hardware components effectively
Certification
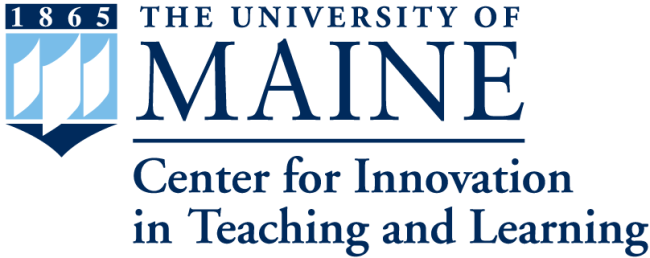
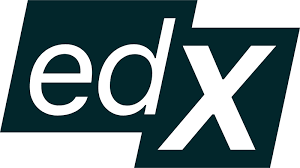