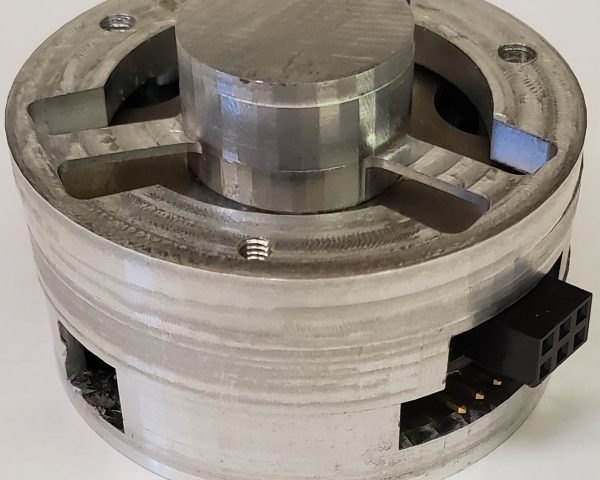
3-dimensional force sensor for gait analysis
Did theoretical and computational analysis to design the sensor and used CAD and CAM software to fabricate using a CNC machine
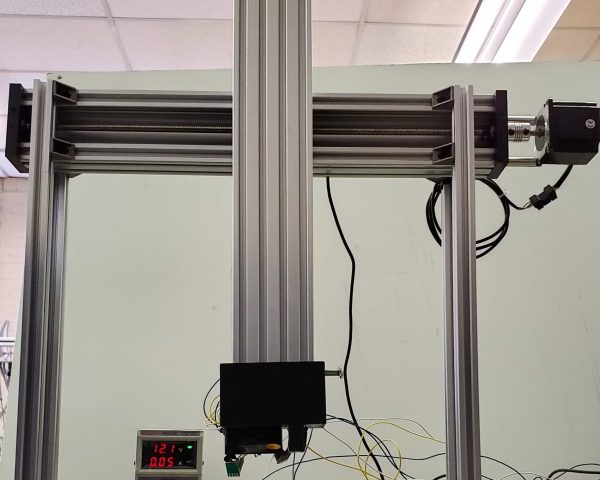
A robotic manipulator for applying 3D force
Designed the end-effector in SolidWorks and built using 3D printer. Used Arduino to collect data from 3 commercial sensors
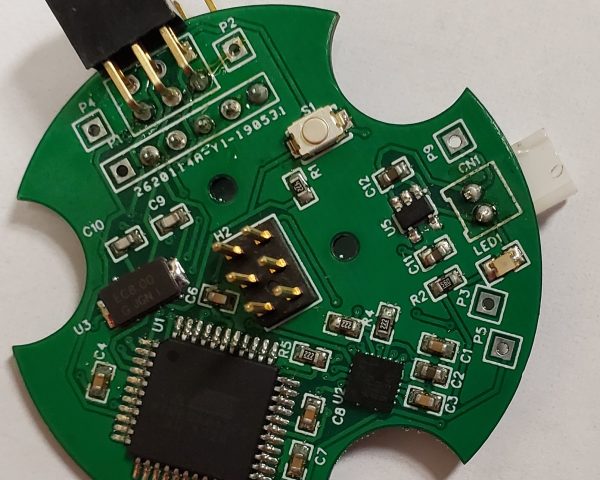
Digital Capacitance Measurement System
Designed the PCB using EasyEDA and programmed microcontroller to collect capacitance data from CDC chip
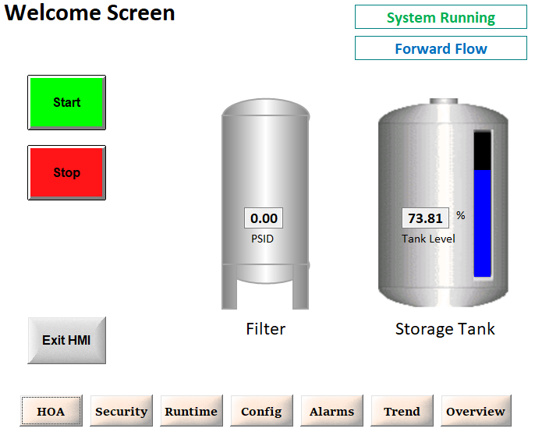
Automation of a water treatment system
Modeled the system using AutoCAD Plant 3d, wrote PLC program using RSLogix, and designed a human machine interface (HMI)
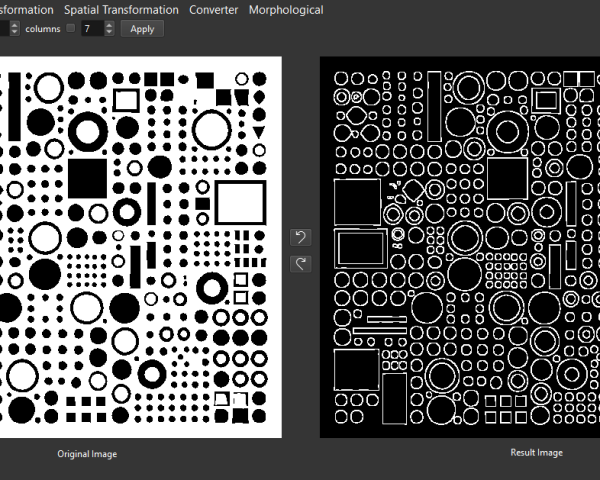
Interactive Image Processing Toolkit
A graphical user interface has been created to use image processing algorithms

IMU Calibration System
Details will be added soon

3D Printed Mobile Robot
Details will be added soon
3D Printed Robotic Arm
Details will be added soon
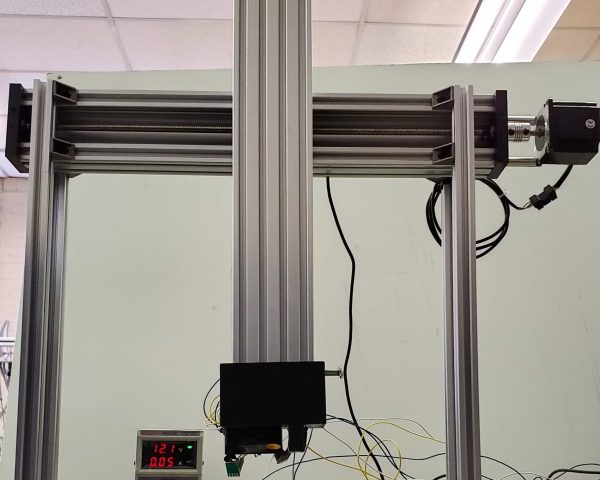
A robotic manipulator for applying 3-axis force
Designed the end-effector in SolidWorks and built using 3D printer. Used Arduino to collect data from 3 commercial sensor
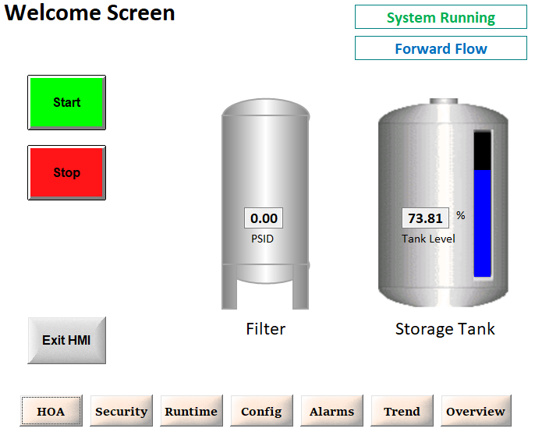
Automation of a water treatment system
Modeled the system using AutoCAD Plant 3d, wrote PLC program using RSLogix, and designed a human machine interface (HMI)
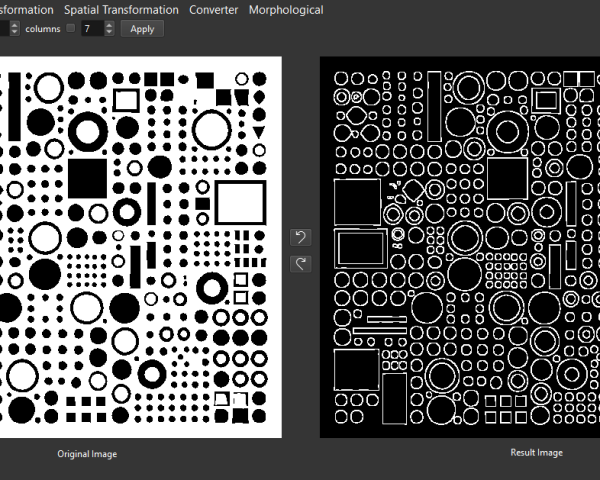
Image Processing GUI
A graphical user interface has been created to use image processing algorithms